Concrete is one of the most widely used construction materials. It is found in everything from residential homes to skyscrapers and commercial buildings.
Commercial Concrete Contractors Dallas TX differs from residential concrete in several ways, including its durability and strength. This article will explore the differences between commercial and residential concrete and how those differences affect different projects.
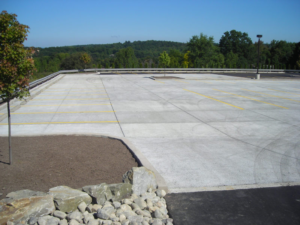
Concrete is an extremely versatile and cost-effective construction material. It’s often used in commercial spaces to create walkways, parking lots, and other structures. Commercial buildings also use concrete for flooring, walls, and other structural elements. Concrete is durable and aesthetically appealing, and it can be stained or colored to add color and style to any building project. However, before you decide to use concrete for your next commercial construction project, knowing how much the process will cost is important.
The cost of commercial concrete varies by region and project type. In general, it’s more expensive in urban areas than in rural areas. The price also fluctuates depending on the availability of raw materials. For example, the steel market is volatile and can cause significant price increases.
A commercial concrete contractor will be able to give you an accurate estimate based on the specifics of your project. They’ll consider the size of your project, the location, and other factors that affect the cost. They can also recommend ways to reduce costs without compromising the quality of the concrete. For instance, adding supplementary cementitious materials (SCMs) can help lower the cost of your concrete while increasing its strength.
Labor is another factor that affects the cost of commercial concrete. A commercial concrete contractor will have a team of experienced workers and specialized equipment to complete the job quickly and efficiently. This helps to keep your project on budget and schedule.
The final cost of your commercial concrete project will depend on the type of work and decorative options you choose. For example, stamped or stained concrete will increase the cost significantly. Selecting a concrete installer with experience and a solid reputation will also help to keep the cost down.
When hiring a commercial concrete contractor, check their credentials and ask for references. Lastly, ensure they have the necessary permits and insurance to complete your project. Also, ask to see examples of their previous work. This will help you determine whether they fit your project well.
Concrete is a durable material that can withstand great wear and tear. It is resistant to tensile and compressive stress, making it an ideal choice for foundations, floors, and parking lots. Concrete is also fire-resistant and has a high thermal mass, which can help lower energy costs in commercial buildings. However, concrete has drawbacks, including its tendency to crack when exposed to moisture or temperature changes.
Commercial concrete contractors use a variety of additives to improve its strength and durability. These include plasticizers, which make the tangible more workable and flexible, and fibers, which strengthen the concrete and reduce its permeability. Additives are also available to speed up the curing process, saving valuable time on construction sites.
The durability of commercial concrete is measured by its flexural and compressive strengths and is determined by testing the material using a simple beam. The flexural strength of the concrete is a measure of its ability to resist bending and deformation, while the compressive strength measures the concrete’s ability to withstand compression.
Although several factors influence the strength of commercial concrete, its compressive strength is often considered the most important factor. The compressive strength of concrete is required for the structural integrity of a building, and a structure that needs this strength will not stand up to a significant amount of pressure.
Commercial concrete mixes are designed to contain the right amounts of cement, aggregate, water, and other ingredients to achieve the desired level of strength. The mixture is then placed in a mold or form to set it under pressure. Aside from adding extra weight to the concrete, this process ensures that the concrete will be poured evenly throughout the entire structure.
The strength of concrete is a crucial part of its performance and is usually rated at an early age. Contractors rely on this information to determine subsequent actions, such as opening roads to traffic and removing formwork from the structural elements of a concrete structure. Achieving a higher level of strength at an early age can also save money, labor, and materials by reducing curing durations.
Commercial concrete has long been lauded for its efficiency and durability, but it also offers businesses an opportunity to enhance their aesthetics with unique design and customization options. From stamped concrete to polished concrete, there are several ways that business owners can use commercial concrete to improve their curb appeal and strengthen their brand image.
For many people, the first impression of a business is its exterior. This is why businesses need an attractive exterior that reflects their brand and appeals to customers. One way to do this is by installing decorative concrete. Decorative concrete is a cost-effective solution that can add a touch of class to any building.
With the help of a skilled commercial concrete contractor, businesses can create unique and visually appealing designs for their commercial projects. For example, concrete can be stained in various colors and patterns to achieve the desired look. In addition, concrete can be carved with tools to add unique designs and logos to the surface. These unique designs will set businesses apart from their competitors and make them stand out.
Adding a water feature to your business is another great way to improve aesthetics. Whether you install a small fountain or a large waterfall, these features can add beauty and peace to any space. In addition, they can also reduce noise pollution and create a more relaxing environment.
The concrete industry has come a long way, and now there are more options than ever for businesses to express their style with this versatile material. Unlike the grey, industrial look associated with traditional concrete, new trends are moving towards what might be described as a natural or organic style. This can include pigmented concrete with earthy hues or surface texture and color created by exposing the aggregate in the concrete.
Polished commercial concrete is a popular choice for modern construction projects. It is available in various finishes and can be used for interior and exterior flooring. Its sleek appearance suits offices, factories, retail shops, warehouses, big box stores, and even private residences. It is also easy to clean and durable, making it an ideal option for commercial spaces.
Concrete is the most widely used construction material in the world. It supports our cities, connects communities, and sustains the global economy. However, it has a significant environmental impact that requires innovative solutions to reduce. Concrete’s primary ingredient is cement, which accounts for 4-8% of global carbon emissions in a climate-change context.
Commercial concrete can be more eco-friendly by integrating recycled materials, energy efficiency, and sustainable production processes. This helps to minimize its initial carbon footprint and maximize long-term sustainability benefits.
These strategies include sourcing local materials, optimizing mix designs, and utilizing industrial byproducts. These resources help conserve natural resources and reduce the need for virgin aggregates. Also, the use of just-in-time production helps to minimize waste and transportation-related emissions.
Innovative concrete technologies also allow for more sustainable building and infrastructure applications. For example, insulated concrete from walls helps buildings consume less energy while paving with eco-friendly recycled asphalt helps to reduce greenhouse gas emissions from cars and trucks.
Moreover, eco-friendly concrete can be recycled at the end of its service life, helping to reduce landfills and incinerators. It can be reused in other construction projects or recycled as aggregates for new concrete mixtures.
The durability of commercial concrete means that it lasts longer, which reduces the need for repair and maintenance work, resulting in savings for building owners. Additionally, eco-friendly concrete is more resistant to damage and extreme weather, which can help lower the risk of structural failure and costly repairs in the future.
Concrete is a durable, lightweight, and versatile material with many commercial uses. It is also affordable and aesthetically pleasing, making it an excellent choice for businesses looking to build or remodel with an environmentally responsible construction process.
While it is important to note that contact with wet concrete can cause chemical burns, commercial contractors should always wear proper safety equipment and follow safe handling protocols. For example, using a protective mask when handling wet concrete is important to prevent skin contamination and eye protection when mixing or pouring. In addition, it is important to clean tools and equipment after use properly.